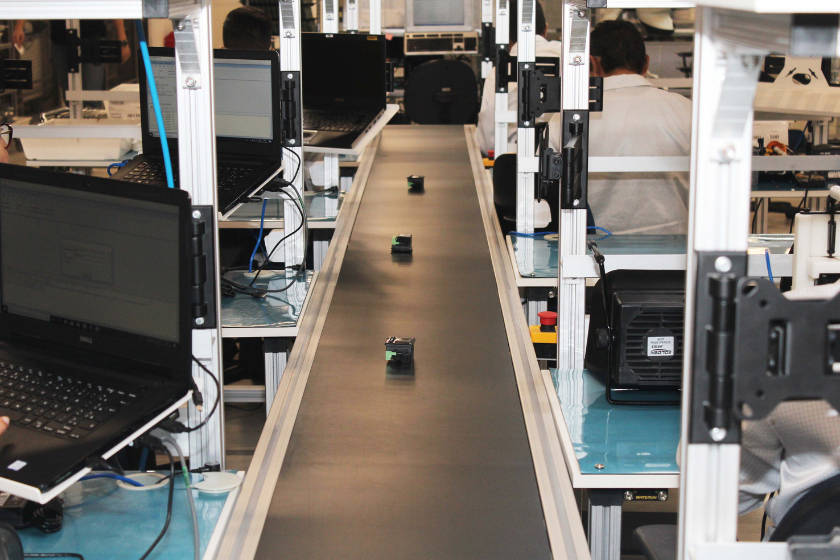
La qualité et la productivité sont des facteurs clés de compétitivité et ont toujours été la préoccupation des secteurs productifs. En effet, quelle entreprise ne cherche pas une productivité de plus en plus élevée sans renoncer à la qualité et à une opération financièrement viable ?
Chercher à améliorer la productivité et la qualité d’une société a pour effet une plus grande satisfaction interne – parmi les collaborateurs – et externe – parmi les clients et fournisseurs –, puisque tous gagnent en matière de prix et de fiabilité en général.
Plusieurs techniques et systèmes de gestion de la qualité sont utilisés dans la cartographie des processus, dans les tests et l’analyse du rapport qualité-prix. Ces outils aident à améliorer tous vos processus et flux de travail, dans le but d’obtenir de meilleurs résultats de productivité, avec une réduction des défauts, délais et coûts.
Et dans l’industrie ? Quels outils peut-on appliquer pour obtenir les meilleures performances sur l’atelier ? Découvrez maintenant les 10 étapes pour avoir une usine à haute efficacité.
1. Analysez vos processus et développez des indicateurs de performance
On ne doit pas se concentrer sur les personnes qui réalisent le travail, mais sur la façon dont elles réalisent leur travail. Normaliser les politiques et les procédures permet de maximiser l’efficacité des processus de production. Formez vos employés de manière adéquate pour que, en plus de l’excellence technique, ils soient fiers de leur travail et recherchent toujours de meilleurs résultats.
Analysez et comparez vos processus actuels pour identifier les problèmes, prédire les résultats et mesurer les gains de productivité à l’aide d’indicateurs de performance clés pour votre usine. Par exemple : mesurez la qualité et la productivité de votre ligne de production, en mesurant le temps moyen d’exécution de chaque pièce et le taux de défauts de qualité à la fin d’un quart de travail.
2. Développez des tests de qualité pour vos processus
Effectuez des tests pendant le processus de production et pas seulement à la fin. Laisser les tests à réaliser à la fin peut élever les coûts en cas de modifications. Si possible, adoptez des tests automatisés qui peuvent être effectués sans intervention humaine et qui aboutissent à des processus de réussite ou d’échec faciles à interpréter, modifier et corriger. Offrir un produit de qualité n’est plus un différentiel ; il est devenu une nécessité. Par conséquent, il est important de maintenir un contrôle strict de la qualité des produits que votre usine produira. Réalisez des inspections de qualité, dans lesquelles l’inspecteur peut identifier et signaler les cas de conformité et de non-conformité.
3. Attention à la gestion des coûts
La gestion des coûts de production est l’une des principales difficultés de la gestion industrielle, mais elle est aussi essentielle pour tenir à jour la santé financière de votre usine et consolider votre opération. Pour maintenir votre usine financièrement viable, vous devez connaître le coût de production de vos produits et prendre en compte plusieurs facteurs qui dépassent les coûts directs. La gestion des coûts peut être assez complexe, donc il est nécessaire de bien étudier ce sujet pour éviter de vendre un produit avec une marge bénéficiaire très faible ou, pire encore, négative.
4. Adoptez une planification et un planning de production par produit
Définissez les heures auxquelles vos ressources (machines et personnes) travailleront. Créez un ordonnancement de production pour enregistrer le temps de fabrication optimal pour toutes les opérations du processus de production d’un produit. Chaque opération a un temps différent et peut être affectée à la ressource qui doit l’exécuter. Une opération peut être réalisée avec ressources différentes, chacune avec son propre délai. Enregistrez avec précision tout ce qui est fait dans l’atelier : les heures de début et de fin, quel employé a effectué le processus de production avec quelle ressource, l’activité effectuée (configuration, arrêt, production) et quel ordre de fabrication a été exécuté.
5. Disposez d’une bonne ingénierie de produit
Une bonne ingénierie des produits est un concept essentiel pour une gestion d’usine d’excellence. Pour ce faire, on doit bien définir la liste des matériaux nécessaires à la fabrication du produit, en planifiant tous les composants requis à toutes les étapes de la production. Créez également un planning complet, couvrant toutes les étapes de fabrication du produit. De plus, il est important de définir les postes de travail dans lesquels le produit passera à chaque étape du planning et combien de temps il restera sur chacune de ces machines. Ainsi, vous saurez exactement quels sont les flux de production. Cela sera essentiel pour réussir à une bonne planification de la capacité de votre usine à l’avenir.
6. Générez des ordres de fabrication pour répondre à la demande de votre industrie
Pour satisfaire ses clients avec excellence et précision, une usine disposant d’une gestion de production efficace doit émettre un ordre de fabrication pour chaque combinaison de produit et délai. Elle est ainsi en mesure de répondre à la demande, qu’elle soit ferme ou prévisionnelle. L’ordre de fabrication doit fournir toutes les informations concernant le projet, en détaillant exactement la liste de matériaux complète, l’ordonnancement et le temps de production. De cette façon, il est possible d’appliquer le concept juste-à-temps, ce qui réduit votre stock de matières premières excédentaires et donne aussi une prévisibilité à vos clients.
7. Contrôlez la réquisition et planifiez les besoins en matériaux
La réquisition de matériel est très importante pour une bonne gestion des stocks, car sans elle, on risque de perdre des matériaux, ou même de les acheter en excès. L’important est que vous ayez le contrôle total des matériaux qui ont été déjà demandés pour un ordre de fabrication et que vous sachiez les différencier du reste de votre stock. Pour atteindre des niveaux de stock optimaux dans votre usine, vous devez mettre en place un plan de production à jour, c’est-à-dire transformer vos commandes client et prévisions de demande en ordres de fabrication spécifiques pour les articles finis.
Avec ces informations, vous pourriez planifier vos besoins en matériaux pour exécuter ces ordres de fabrication en différentes quantités et délais. En bref, créer un plan d’achat et d’utilisation des matériaux qui répondra à votre production dans les délais et la quantité exacts.
8. Enregistrez la production réalisée et livrée
Lorsque la fabrication de votre produit est finie, il est important de créer un enregistrement de cette production qui détaille tous les matériaux utilisés. Ainsi, ils seront supprimés de votre inventaire d’articles en production ou en processus. Lorsque vous générez des ordres de fabrication, commandez les matériaux et enregistrez la production réalisée de manière efficace, votre industrie sera prête à contrôler le stock de produits finis, semi-finis et de matières premières.
9. Prenez des décisions basées sur les statistiques
Après avoir organisé votre production, défini l’ingénierie de produit, organisé les stocks, suivi la production et mesuré la qualité, il est temps de mesurer le résultat de toutes les étapes. L’analyse des données est la dernière étape pour atteindre l’excellence dans la gestion industrielle de votre usine. Ici, vous devrez adopter un système capable de générer des indicateurs de performance avec les résultats de votre usine. Avec ces indicateurs, il sera facile de gérer les données et de prendre des décisions.
10. Écoutez le feedback
Mesurez la qualité et les gains en productivité sans oublier de rapporter les chiffres à l’accroît de la satisfaction client. Recueillez les feedbacks des employés, des clients, des fournisseurs et des partenaires d’affaires pour obtenir leur avis sur vos produits ou services. Utilisez le feedback des clients pour améliorer vos produits actuels et définir le développement de nouveaux produits.
L’importance d’optimiser la gestion de la production en usine
En adoptant les dix étapes présentées, vous améliorez la gestion de votre entreprise et, par conséquent, la productivité. Parmi les principaux avantages obtenus, on remarque :
- Détection des goulots d’étranglement : les défaillances qui passaient inaperçues seront désormais détectées, optimisant ainsi le temps nécessaire pour y apporter des corrections et améliorations ;
- Contrôle du processus de production : le manager aura une vision plus globale de l’industrie et une connaissance plus précise du fonctionnement des processus ;
- Standardisation : les opérations réalisées par les collaborateurs et les processus industriels seront standardisés ;
- Meilleure qualité produit : grâce à la standardisation, on garantit que toutes les activités maintiennent un niveau élevé, ce qui répercute positivement sur la qualité du produit ;
- Augmentation de la production : la réorganisation des processus réduit la bureaucratie et les coûts, en plus de permettre la meilleure exploitation des opportunités, dynamisant ainsi la production.
Typiquement, les usines deviennent plus compétitives et efficaces au fil du temps. Les entreprises qui ne cherchent pas à optimiser leurs processus perdent leur position sur le marché et deviennent obsolètes. L’excellence dans la gestion de la production est également importante pour la survivance de l’entreprise en périodes d’adversité, comme les crises économiques ou même pendant la pandémie de la Covid-19.